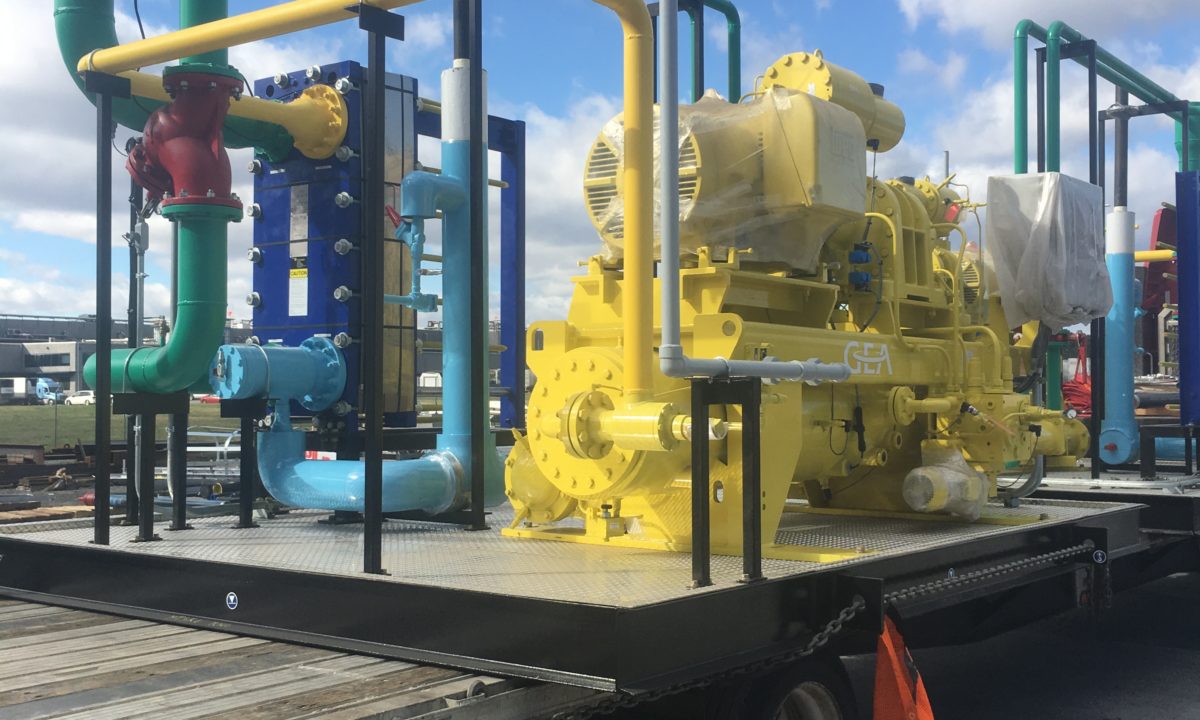
Building an Extreme Testing Facility
Innovative is proud to announce the completion of an environmentally friendly ammonia refrigeration system in Dearborn, Michigan. The installation will support our client’s operations for the next 30-50 years, using natural refrigerants. The system will test engines and powertrains in extreme conditions, all the way down to -55°F.
Innovative began the design process two years ago. We worked closely with architect Albert Kahn Associates, construction manager Barton Malow, and the client to design and engineer a state-of-the-art ammonia/CO2 cascade system. Our Director of Engineering worked diligently with Malow’s Chief Engineer to minimize the ammonia charge.
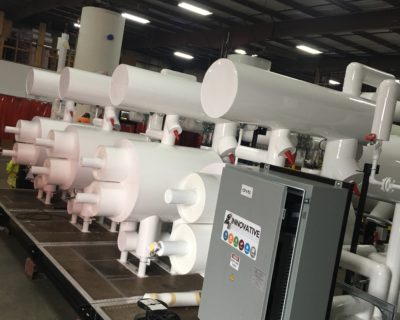
Nearly a year into the project, Innovative moved into the manufacturing phase. In the eight months that followed, we produced seven ammonia skid packages, 12 reciprocating compressors, a cascade condenser platform with four cascade condensers, eight remote chiller packages, and a length of prefabricated pipe to construct the project. Everything was built to ASME B31.5 and IIAR2 2014 specifications.
Electrically, there is a fully integrated Allen-Bradley PLC system with state-of-the-art HMI graphics and a 3D interface. Variable speed drives were included to allow for superb turn down control at low and partial loads. Innovative also provided our cloud-based ePSM program to facilitate daily operations, training, and regulatory compliance.
The chilled water system can produce 1,300 tons of chilled water. It was designed with an ammonia charge as low as 0.99 pounds per horsepower. The ammonia/CO2 cascade system has an ammonia charge even lower, at 0.89 pounds per horsepower.
We moved into the construction phase last December. Our union superintendent on site led 15 welders, installing more than 6,000 feet of pipe, 12 electricians and eight insulators. Safety is a top value for Innovative–we provided a dedicated, full-time, on-site safety manager for the project.
Small doors didn’t stop us from building a large system. Since the packages had to go into an existing facility, they were designed to be “knocked down” to fit through existing doorways and small openings, then reassembled in their final location.
The client is now in the commissioning phase and is about 90 percent complete. Phase 2 (-64°) will be completed this month, and Phase 3 (-45°) is projected to wrap up in the beginning of October.
Innovative is working closely with the client’s engineering and maintenance teams to provide hands-on, in-depth training. We look forward to turning over daily operation to the client very soon!