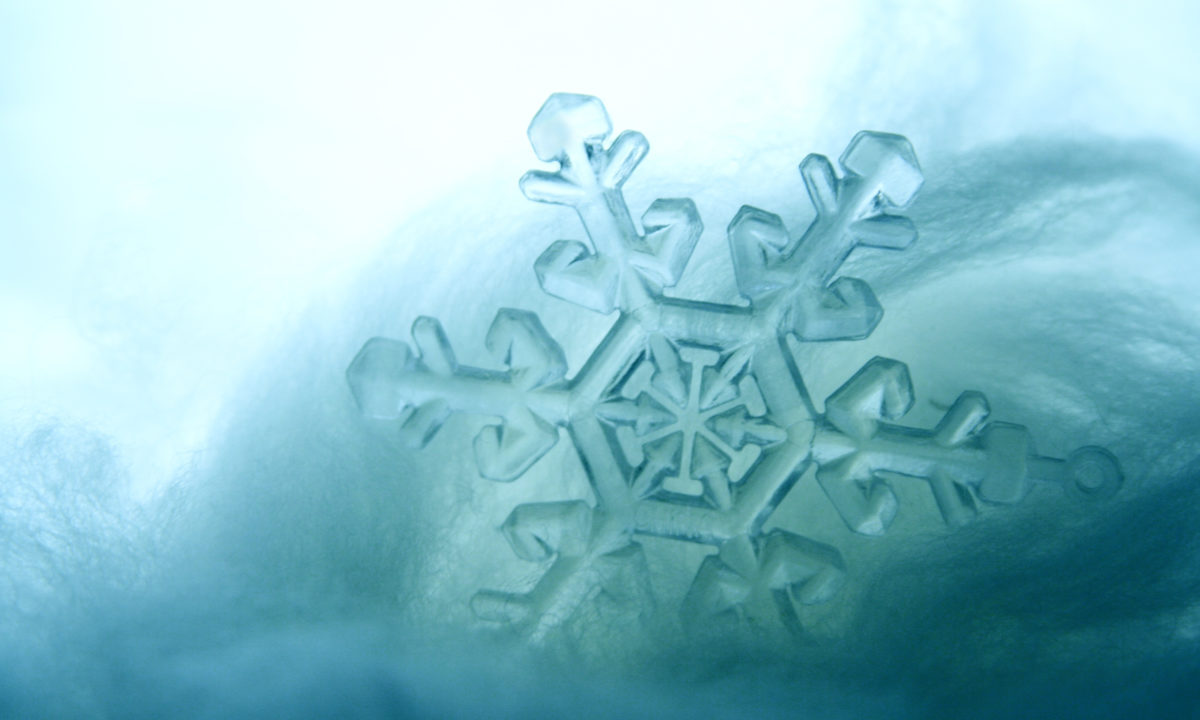
Optimizing Refrigeration Systems During Winter
Industrial refrigeration systems are designed to maintain temperature during the warmest days of the year–on those days, refrigeration systems are operating under maximum load.
But during the cooler days of the year, refrigeration systems operate under less strenuous conditions. They operate under partial load, or “part load.” Part load conditions can be broken down into two types:
Types of Part Load
- Less heat in the refrigeration system (or less heat removal from the area).
- More favorable ambient conditions for the evaporative condenser.
During colder months, cold storage warehouses would see both types of part load conditions. Production facilities, on the other hand, would only see the second type–although any storage areas or docks attached to those facilities may see the first.
Winter temperatures can present challenges for facilities (such as freezing water lines), but the part load conditions that they bring can present opportunities to increase efficiency. We go over four such strategies below:
Strategies to Increase Energy Efficiency during Winter
- Operate at lower condensing pressures saving energy at the compressors.
- Use compressor sequencing.
- Optimize evaporator conditions.
- Extend run time between defrosts.
1. Operate at Lower Condensing Pressures
Operating at lower condensing pressures can be a good strategy to increase efficiency. The goal is to operate the evaporative condenser “wet” (pumps running) rather than “dry” (only fans running), while avoiding potential pitfalls such as frozen water lines, frozen water in pumps, or ice buildup in condenser sumps.
For systems with an integral sump with an automatic water drain/refill feature, or a remote sump with pump cutouts, set these to the lowest reasonable temperatures. If manual draining and refilling is required, then be as vigilant as possible to operate the condenser wet.
When pumps and fans are operating during lower wet bulb temperatures, the evaporative condensers will likely have the capacity to lower condensing pressures below the “minimum pressure.” To give an absolute minimum, some systems can operate at 85 psig (56℉ ammonia). (This of course wouldn’t be practical in areas such as Miami, FL.)
How to Find the Right Pressure
- If you have hot gas heating with a float drainer at the heating unit, you will find the limit when the room can’t stay warm enough.
- If you have hot gas heating with a pressure regulator valve at the heat unit, you will also need to set the valve to the proper pressure for the room’s temperature.
- For hot gas defrost try setting the pressure regulating valve at 70psig or lower and adjusting defrost timers for proper defrosting. A regulator pressure of 70psig should allow proper defrost with the condensing pressure as low as 85psig or 90psig.
- If you have a hot gas compressor, use it and check that any discharge pressure control algorithms are set properly and are working properly.
- If you have wet bulb control, make sure the ambient temperature and humidity sensors are calibrated and functioning properly. Also make sure the approach is a reasonable value for your system (20℉ is likely too high and 5℉ is likely too low). Keep in the mind that the goal of wet bulb control is to minimize the combined energy usage of the condensers and compressors.
- As with any time of the year, be sure the auto purger is functioning properly and that you do not have air in the system.
There are several misconceptions about lowering condensing pressure. Try not to let any of these hold you back.
Common Misconceptions when Lowering Pressure
- Tradition. Just because you have always set the minimum at 120psig doesn’t mean that the minimum should be so high.
- Fixed Volume Index (VI). Lowering condensing pressure will lower compressor power consumption even without variable VI or stepped VI.
- Insulated freezer floors that have underfloor glycol heated by hot gas. A misconception might be that the glycol must be at least 55℉ to keep the floor from heaving.
A few limitations to lowering condensing pressure to 85psig or 90psig that would require system upgrades might be TXVs for DX evaporators, TXVs for liquid injection oil cooling, or oil separators that were not oversized to prevent excessive oil carryover.
2. Compressor Sequencing
With less heat moving into the system, compressors don’t need as much capacity. Instead of just running the same compressors with unloaded slide valves or slower speed, try the following:
- If you have compressors of different sizes, operate the smaller ones and turn off the larger ones.
- If you have economized compressors, try operating the economizers and having one of the high temperature compressors turn off. Some systems with low enough high temperature loads during winter, can operate effectively with only economizers and no high temperature compressors.
As always with compressor sequencing, be sure the most efficient part load compressors are trimming (such as screws with VFDs or reciprocating compressors with cycling unloading).
3. Optimize Evaporator Conditions
Evaporators need to remove less heat from areas so take advantage of this fact. With VFD fans and multiple evaporators in a room, use group control so the liquid lines stay on and fan speeds can be lower. Raise the compressors’ suction pressure because the evaporator TD can be lower.
Perform less frequent defrosts (see below).
4. Extend Run Time between Defrosts
Winter conditions bring dryer air. Dryer air means evaporator coils build frost less quickly. This leads to optimization as simple as extending the liquid run time between defrosts. Of course, when more humid weather returns at some point in spring, be sure to return the timers to your previously optimized settings.
You may realize that some of the above will also be good practices for spring and fall optimization so apply as often as is possible.
Take control of your facility with our eInnovative platform, a full suite of tools designed to manage your facility. More information is available here.